Notch Milling Machine
For Highest Precision and Efficiency
For accurate machining of structural steels of diameters up to 80 mm, Herkules offers a high-performance notch milling machine. More than 200 notch milling machines have been delivered to satisfied customers all over the world.
Excellent damping parameters and outstanding rigidity – these are the main characteristics of our notch milling machines NNF. An almost vibration-free machining is guaranteed. The outstanding quality of each single component manufactured in-house increases the operational life of the machines significantly. A powerful milling spindle guarantees a strong performance and short machining times.
High efficiency thanks to reduced set-up times: the rotating counter bearing base components, which can accommodate four counter bearings with identical or different diameters, are swivelled in as required, allowing for a speedy and accurate change of milling diameters. This is how Herkules significantly reduces set-up times.
Technical Data
Maximum Performance and Precision
For up to 3,500 rolls per month
Roll diameter max.
500 mm
Groove size max. 80 mm
Roll length max. 2,500 mm
Roll weight max. 2,000 kg
Industries
For Complex and Individual Demands
Herkules has been an established partner to a wide range of industries for many decades. Based on this extensive know-how, Herkules has developed individual solutions for every branch of industry. With a Herkules machine, every industry lays the foundation for a high-quality end product.
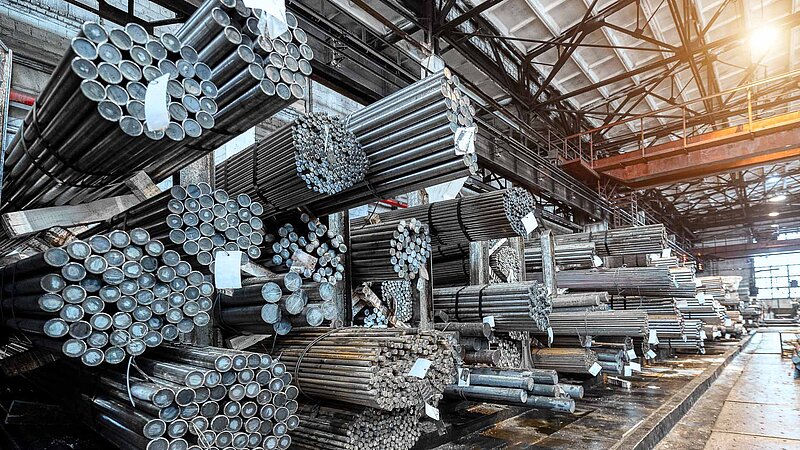
Technology
Developed to Your Individual Requirements
The design of the Herkules notch milling machine NNF is characterized by high-quality machine components. Headstock, tailstock, the bed and the milling saddle are made of cast iron and machined to the highest precision within the company group.
The reinforced Herkules milling saddle allows for the smooth machining of notches with diameters of up to 80 mm. By the help of the specifically developed control KP 20, all kinds of different notch forms can be produced.
Based on many years of experience, Herkules adjusts each single machine to the specific needs of the customer. A wide range of Herkules equipment options serves to find the perfect solution for your individual machining task.
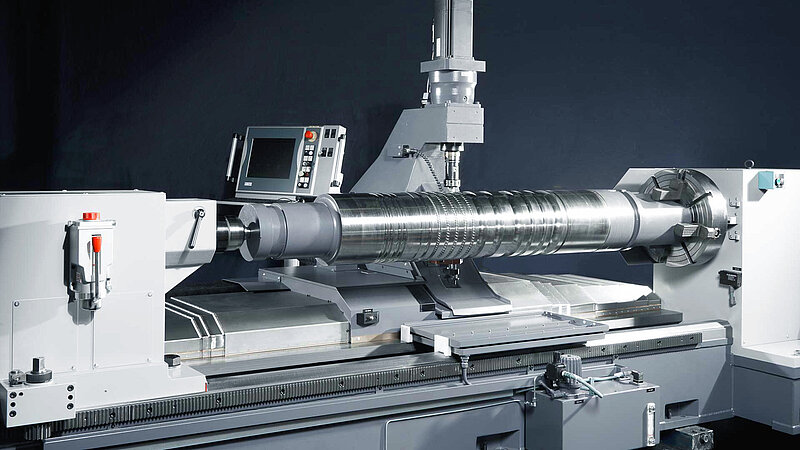